Get that 'learning' done now - while you still have access to qualified instructors.
Start with Oxy-Acetylene, not Arc, not Mig, Not Tig
While you CAN cut with an arc-welder and appropriate attachments - it's not for beginners,and is more expensive than gas.
Equipment- a PROFESSIONAL level Victor welding,cutting set with hoses. Not the junk at Home Depot or Lowes.
Tanks - purchase - do not rent. Large acetylene tank (3 footer - there are larger sizes, but those are for big/huge jobs. Oxygen tank - at least the 5' tall tank. Get a good dolly to use them with, with big STEEL wheels (not plastic). A welding supply store will get you going there - get a good HELMET (not goggles) with appropriate shades (changeable) for oxy welding, and also different (darker) shade lens for arc. Helmets are far better for hard work than goggles. Get your welding gloves at the welding supply also, chipping hammer, and brushes. The professional quality at a supply house will be worth the higher prices, tools that last. Avoid those small welding rigs with tiny tanks - they are pretty worthless, especially on a farm.
Why get instruction NOW ? Because you are much closer to the oil field and other industries that have heavy experience professionals around that can teach.
I was fortunate in getting a world class instructor while still in high school. He taught at the local Junior College, which required me to jump thru hoops with the high-school admin to allow me to take a college level class. Eventually bypassed them by taking the course on an 'audit' basis.
The instructor's qualifications ? Well - during WWII he was in the Pacific - maintenance on P-51's and other equipment. He learned to weld aluminum with Oxy-Acetylene on the nose-cones of the P-51's. Now, not many welders can weld aluminum with Oxy-Acetylene - it's a lot tougher than it looks. He worked in the mining industry - where just to start a job they would take down a hundred pounds of brass (lot of cast-iron equipment down there) just to start. And then - a few decades in the oil fields - where code welding is an absolute requirement. The guy was an absolute genius with metals, and also an artist extraordinaire. He made sculptures, not by 'joining' pieces together, but by starting with a puddle, and building that puddle, one bead at a time, up into the finished piece. Several pieces were flowers, with leaves, stems, thorns, horses, cowboys on horses - in different metals - and then 'coloured' by etching with different chemicals and acids. Absolutely exquisite.
Anyway - THAT was the level of instructor that I had access to - and he taught as well as he welded. All the oil field, and Lubbock Tank Manufacturing, and other industries in West Texas sent their welders to him- his graduates could weld 'to ASME code'. I did not reach that level - but my welds, brazes, cutting abilities are far better than most of the so-called welders that work at local shops (auto, etc) can do.
And my welds are structurally solid.
Once you have mastered Oxy-Acetylene techniques, THEN , and only then does one start learning arc welding. It is too easy to get really lousy welds in arc welding that 'look ok' but actually have no integrity. The fundamentals of gas welding teach you how to join metals, both similar and dissimilar.
MIG (mostly inert gas) and TIG (total inert gas), and Wire welding are simply extensions of good arc welding - and are easily learned after mastering Oxy and arc techniques.
A good instructor will assign you a solid Welding Manual (read - encyclopedia) that will be useful forever, covering the wide variety of info on steels, casts, brasses, bronzes, and maybe even some of the exotics with technical information that one must have in order to properly weld, braze, solder, cut, temper and otherwise work with metals.
BTW: Make durn sure that you learn (from your GOOD instructor) how to work on cast iron. Brazing is but one technique. Cast irons have different levels of carbon in them, which make for a lot of variety of different problems in working on them. Cast is more difficult to work on than steel - but is EXTREMELY common in many pieces of machinery - especially farm machinery. Engine blocks and heads can be very tricky, and the older they are, the more difficult they can be.
Welding, for me, is a very rewarding activity.
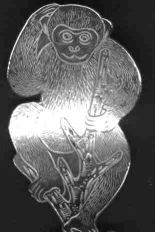
Finally, brethren, whatsoever things are true, whatsoever things are honest, whatsoever things are just, whatsoever things are pure, whatsoever things are lovely, whatsoever things are of good ...